Key Trends in Pharma for 2025: AI, Flow Chemistry, and Advances in Ophthalmic Drug Delivery
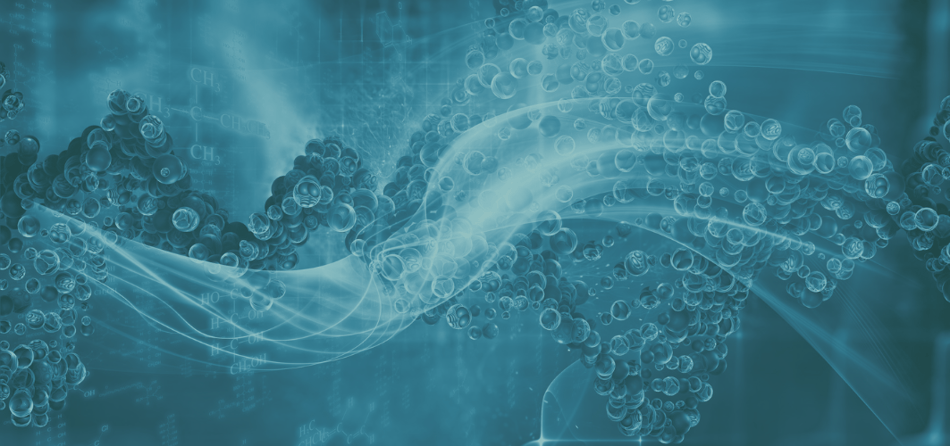
As we kick off 2025, pharmaceutical manufacturing continues to change dramatically.
Emerging technologies and shifting priorities in research and development are reshaping how drugs are discovered, manufactured, and delivered. While these changes bring exciting opportunities, they also pose complex challenges for pharmaceutical companies.
In this post, we’ll take a closer look at these exciting trends and how they’re poised to reshape the industry.
How AI is Revolutionizing Drug Discovery in 2025
Artificial intelligence is increasingly becoming an integral part of pharmaceutical development, unlocking new possibilities in drug discovery. We recently spoke to Dr. Kevin Hunt of Vanqua Bio to learn more about how AI is reshaping this process, and Dr. Hunt was enthusiastic about its potential impact.
“I think AI will be on the desk of most medicinal chemists—and not just on the desk, but actually in the form of a useful desktop app—in the next 5 years,” he said.
This sentiment is echoed by a recent Infosys survey of pharma and life science professionals, where 90% of respondents agreed that AI is crucial to their company's success. Of those, 40% have already deployed AI solutions, with 76% leveraging big data automation, 64% using machine learning, and 60% applying predictive analytics.
While machine learning has been a fixture in chemistry for years, the difference now lies in accessibility.
"Machine learning's been used in chemistry for decades, but what's different now is that the newer models in AI allow you to do this on your PC. It's a lot more sophisticated, but with a lot less heavy lifting,” Dr. Hunt said.
The democratization of AI enables smaller labs to innovate while also reducing human bias in data interpretation. “If you feed it the right data set, AI does that better than humans, in my opinion,” Dr. Hunt said. This capability is helping pharmaceutical companies improve patient population analysis, pathway identification, and ultimately the discovery of promising drug candidates, particularly for rare diseases.
Despite its potential, however, AI still faces significant challenges in drug discovery.
“Making a drug is all about three-dimensionality. The quality of the data coming in, the numbers, even the biological activity associated with those molecules is often poor or not well reported. So that part, the early part of drug discovery, is still more of a blunt tool because you're not able to feed the machine well.”
To overcome these challenges, it’s critical to strike the right balance between machine predictions and human expertise. “Artificial intelligence is great, but real intelligence—human intelligence—is even better,” Dr. Hunt said, highlighting the importance of collaboration with partners who can complement AI tools with practical problem-solving experience.
“If they have AI helping them, that’s fantastic, but ultimately, when I’m reaching out to a partner, I’m still looking for problem-solving experience.”
Continuous Flow Chemistry in Pharmaceutical Manufacturing: Why It’s the Future
Continuous flow chemistry is rapidly gaining traction as companies look for more efficient and adaptable methods. Unlike batch processing, where all reagents are added at once, continuous flow chemistry involves feeding reagents into a reactor at a controlled rate. As Dr. Gamil Alhakimi, CEO and Co-Founder of GL CHEMTEC, recently explained in our discussion on continuous flow chemistry, “Chemical reactions occur in a continuously flowing stream rather than in isolated, discrete batches."
This process offers several key advantages that drive its growing adoption in the industry:
Key advantages of continuous flow chemistry
- Enhanced control: Continuous flow chemistry allows for better control over critical reaction parameters such as temperature, pressure, and residence time. “This leads to more consistent and reproducible outcomes,” Dr. Alhakimi explained.
- Improved safety: The process enables safer handling of hazardous materials, as only small quantities are processed at any given time.
- Increased efficiency: “Flow reactors enable rapid mixing and efficient heat transfer, significantly decreasing reaction times—some processes that took hours can now be completed in minutes,” Dr. Alhakimi explained.
- Sustainability: Flow chemistry uses fewer reagents and solvents than batch processing, with steady-state conditions contributing to more efficient energy use.
For companies considering this transition, Dr. Alhakimi advised a gradual approach: “Start with small-scale pilot projects and focus on optimizing the entire process flow, not just replacing batch processes.” He also recommended leveraging automation, AI, and real-time monitoring to maximize the benefits of flow chemistry.
Finally, Dr. Alhakimi emphasized the importance of collaborating with contract development and manufacturing organizations (CDMOs) for successful implementation.
“The benefits of investing in innovative CDMO partners like GL CHEMTEC always become evident over time,” he said.
Emerging Innovations in Ophthalmic Drug Delivery for 2025 and Beyond
As demand for ophthalmic treatments continues to rise, 2025 and beyond will see a strong focus on emerging innovations in drug delivery systems. Researchers and manufacturers are increasingly exploring new ways to address the unique challenges of delivering drugs to the eye. These efforts are particularly critical in overcoming the barriers that impede effective drug absorption, and several key trends are shaping this space.
Dr. Wolf Nickel, a leading expert in the field and a member of GL CHEMTEC’s Scientific Advisory Board, recently highlighted the major barriers hindering efficient ophthalmic drug delivery:
- Lipid barrier: The eye’s lipid-rich surface impedes the absorption of drugs.
- Charged bipolar barrier: The cornea’s unique structure presents additional challenges for drug penetration.
- Cornea: The cornea itself is a critical barrier to effective drug delivery.
Key Trends in Ophthalmic Drug Delivery
Several emerging trends are shaping the future of ophthalmic drug delivery, and they represent critical areas of innovation for 2025 and beyond:
- Improving penetration or adhesion
One of the primary areas of focus in current ophthalmic drug delivery is improving the penetration and adhesion of drugs to the ocular surface.
“The biggest challenge is finding ways to improve how drugs are absorbed and processed within the eye,” Dr. Nickel said, explaining that this is pushing research and development of solutions that improve the pharmacokinetics of eye drops. “This means improving drug absorption, prolonging residence time, and achieving targeted delivery." - Leveraging specialized excipients and polymers
A key trend driving advancements in ophthalmic drug delivery is the development of specialized excipients and polymers. Dr. Nickel highlighted how the precise tailoring of these components is crucial to creating effective drug delivery systems:
“The chemistry of the drug delivery system needs to be carefully tailored. Do you want it to be lipophilic, more polar, or even enzyme-linked so it can be cleaved off at a specific location? All of these factors depend on where the drug needs to be delivered within the eye and what the sponsor requires.”
This tailoring, he explained, is essential for enhancing the bioavailability and stability of drugs used in eye treatments. By collaborating with CDMOs like GL CHEMTEC, pharmaceutical companies are increasingly able to refine their in-house expertise in excipients and polymers, ensuring that these systems are optimized for overcoming the inherent complexities of ocular drug delivery. - Antibody-drug conjugates (ADCs)
ADCs are transforming ophthalmic treatments, particularly for chronic eye diseases, by enabling targeted, sustained drug delivery. Dr. Nickel shared insights into two significant ADC developments:- Pullulan-dexamethasone conjugates, which combine corticosteroids with polysaccharides to create a sustained-release system for treating eye diseases, significantly extending the therapeutic window.
- Dendrimer conjugates, which are nano-sized particles that, when paired with drugs like fluocinolone, can maintain therapeutic levels for up to 90 days, reducing the need for frequent injections.
These advances rely on the strategic use of lipophilic components as carriers. “Lipophilic components help drugs navigate the eye's natural barriers,” Dr. Nickel said. “Once at their destination, enzymes transform these molecules into more polar forms, enabling precise interaction with the target tissue.”
These ADC advancements offer significant promise for ophthalmology and may also extend their impact across other therapeutic areas, ushering in a new era of targeted treatments across medicine.
GLC: Your Trusted CRO/CDMO Partner
GL CHEMTEC is passionate about your success and committed to solving your most complex chemistry challenges. We offer fast, flexible, cutting-edge solutions to take your medicinal chemistry and early-stage small-molecule routes to the next level.
GL CHEMTEC provides:
- A secure North American alternative to overseas providers, offering R&D labs, Kilo labs and scale-up facilities in the Greater Toronto area
- Expert custom formulation development for pharmaceutical and medical device applications
- A local partner who will ensure secure shipping, real-time communication and the highest levels of IP protection for your early stage work
- A highly customer-centric culture with a 20+ year track record of success
- ISO 9001:2015 and ISO 13485:2016 certifications
- A GMP compliant cleanroom with GMP Reactor Suites coming online soon
Contact GL CHEMTEC to learn how we can help you integrate cutting-edge technologies into your R&D today.