Continuous Flow Chemistry in Pharmaceutical Manufacturing: Why Leading Companies Are Making the Shift
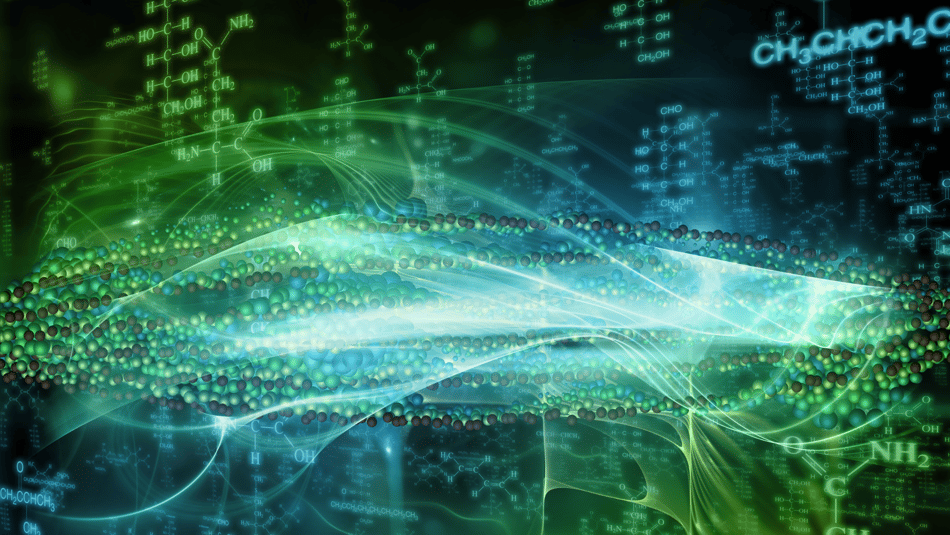
As traditional batch processing struggles to keep pace with the pharmaceutical industry's evolving demands—such as speeding up drug development, reducing costs, and enhancing sustainability—manufacturers are increasingly turning to continuous flow chemistry as a faster, safer, and more efficient alternative.
In fact, the global flow chemistry market is projected to grow at a CAGR of 11.24% over the next five years, reaching a market value of $3.73 billion by 2030.
We recently spoke with Dr. Gamil Alhakimi, CEO and Co-Founder of GL CHEMTEC, to explore how continuous flow chemistry is transforming drug development and why leading companies are embracing this increasingly popular technology.
Continuous Flow Chemistry vs. Traditional Batch Processing
The main difference between continuous flow chemistry and traditional batch processing is in how reactions are conducted. Batch processing involves conducting reactions in a single vessel, where all reagents are present from the start and processed sequentially. By contrast, in continuous flow chemistry, reactants are continuously fed into a reactor, allowing them to mix and react as they flow through the system.
“Continuous flow allows for better control over reaction conditions, such as temperature, pressure, and residence time, leading to more consistent and reproducible outcomes,” said Dr. Alhakimi.
He added that continuous flow provides a number of additional advantages over batch processing, including:
- Minimized downtime between batches, resulting in higher efficiency and throughput
- Improved heat and mass transfer, as better control of reaction conditions can lead to faster reaction times and higher efficiency
- Enhanced safety, as smaller quantities of hazardous materials are processed at any given time, reducing the risk of dangerous reactions.
“Continuous flow handles reactive materials more safely by processing small amounts at a time. This minimizes the risks of dangerous reactions, which is crucial for hazardous intermediates in drug production,” Dr. Alhakimi said.
How Leading Companies Are Leveraging Continuous Flow Chemistry
Pharmaceutical manufacturing leaders are increasingly leveraging continuous flow chemistry to enhance efficiency, reduce costs, and drive innovation.
Here’s how they’re doing it:
- Real-time monitoring and automation: Continuous flow systems typically use advanced automation and AI for real-time adjustments. “With continuous flow, we can monitor and adjust every parameter in real time. This level of control not only ensures higher quality but also significantly reduces the risk of human error,” explained Dr. Alhakimi.
- Microfluidics and miniaturization: “Microfluidics in continuous flow systems give us the ability to experiment with complex reactions in a controlled environment,” Dr. Alhakimi said, adding that continuous flow is ideal for high-throughput screening and rapid synthesis, as it enables precise control over small volumes, which can accelerate drug development.
- Multistep synthesis integration: Continuous flow systems could integrate multiple reaction steps into one process, which is a “game-changer,” according to Dr. Alhakimi.
“It cuts down on the need for intermediate handling and purification,” he said. - Improved kinetics and yields: Continuous flow systems provide a much higher level of control over reaction kinetics.
“We can fine-tune every aspect of the reaction, from temperature to flow rate, which can optimize yields and ensure we’re getting the most out of our raw materials,” Dr. Alhakimi said.
Flexibility and Scalability in Continuous Flow Chemistry
Continuous flow chemistry is an ideal solution for companies looking to scale production efficiently. To start, continuous flow systems are easily scalable as they can adjust flow rates or operation times, enabling a smooth transition from lab-scale experiments to large-scale manufacturing.
“For pharmaceutical clients, this translates to faster development times, lower costs, and quicker market entry for innovative therapies,” said Dr. Alhakimi. He added that this is further enhanced by the fact that continuous flow chemistry is adaptable to various reaction conditions and advanced techniques.
“Flow systems can incorporate electrochemical and photochemical processes, broadening the range of feasible reactions,” he said.
Continuous Flow Chemistry and Sustainability
Continuous flow chemistry aligns with the growing emphasis on sustainability and green chemistry in the pharmaceutical industry, as it enables:
- Safer handling of hazardous materials: “Continuous flow chemistry inherently minimizes risk. By processing small quantities at a time, we can safely scale up reactions that would otherwise be too hazardous,” Dr. Alhakimi explained.
- Reduced waste and environmental impact: Continuous flow systems use reagents more efficiently, which “aligns perfectly with our green chemistry initiatives. By reducing waste and improving efficiency, we’re able to lower our environmental footprint while still delivering high-quality products,” Dr. Alhakimi said.
How to Transition to Continuous Flow Chemistry
If you’re considering transitioning your manufacturing process to continuous flow chemistry, here are a few key steps Dr. Alhakimi suggested to ensure a smooth transition:
- Start with small pilot projects: Implement continuous flow chemistry through small-scale pilot projects, which will allow you to gain experience and fine-tuning processes before scaling up.
- Invest in expertise: Train staff or hire experts in flow chemistry to build in-house expertise. This will facilitate a smoother transition and long-term success.
- Optimize the entire process: Focus on optimizing the entire workflow, not just replacing batch processes, as this will maximize efficiency, scalability, and sustainability.
- Collaborate with industry partners for expertise and technology: Partner with industry leaders, academia, and technology providers to accelerate adoption and gain access to innovations like automation, AI, and real-time monitoring. These partnerships will optimize reactions, enhance product quality, and streamline the transition to flow chemistry.
- Address regulatory considerations: Early understanding and management of regulatory requirements specific to flow chemistry are crucial for ensuring smooth adoption and compliance.
GLC: Your Trusted CRO/CDMO Partner
GL CHEMTEC is passionate about your success and committed to solving your most complex chemistry challenges. We offer fast, flexible, cutting-edge solutions to take your medicinal chemistry and early stage small molecule routes to the next level. Our commitment to a collaborative partnership means we scale and adapt precisely to meet your evolving needs.
GL CHEMTEC provides:
- A secure North American alternative to overseas providers, offering R&D labs, Kilo labs and scale-up facilities in the Greater Toronto area
- Expert custom formulation development for pharmaceutical and medical device applications
- A local partner who will ensure secure shipping, real-time communication and the highest levels of IP protection for your early stage work
- A highly customer-centric culture with a 20+ track record of success
- ISO 9001:2015 and ISO 13485:2016 certifications
- A GMP Cleanroom with GMP Reactor Suites coming online soon